Innovation in Quality tools for a stand alone eye hospital
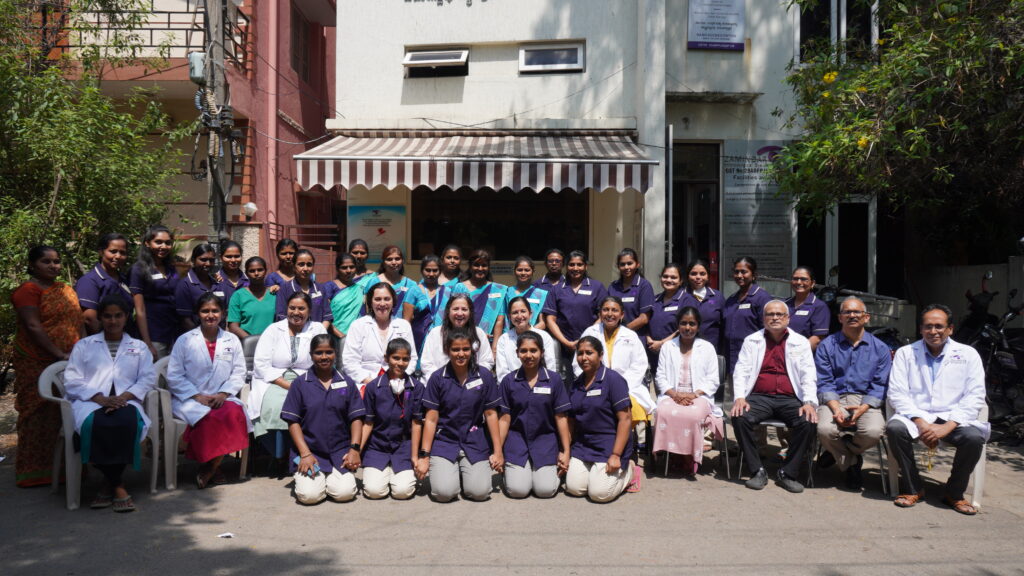
Implementing continuous quality improvement standards is a challenge for most of the stand
alone eye hospitals . More often than not, documentation outweighs implementation.
We were able to put innovative ideas to work and were able to bring core benefits across the
organisation. We will highlight the innovative ideas we have successfully implemented for a
more involved staff.
We involved our employees in all aspects of quality improvement. We started off by asking
employees to write their own SOP, preparing process protocols, communication videos,
presentation on use and maintenance of equipments. This not only helped in training of staff
but also gave them ownership of SOP and this in-turn ensured maximum implementation.
We also introduced the Japanese Management principles like 5S and Kaizen.
- The basic 5S that is Sorting, Straightening, Shining, Standardizing and Sustaining
helps in reducing clutter, know exactly where all things are stored hence time spent
on searching and duplicating work is reduced. - Understanding, writing and following Standard Operating Policies has been a gamechanger in our center. Some of our employees are with us for 10-15 years.
Knowledge and processes were available with them. Defining and standardizing each
activity resulted in a exhaustive process mapping. This was done by the employees
themselves. This made them the owners of the SOP which resulted in
• Maximum implementation
• Motivated staff - New staff are trained faster and systematically
- Less error
- More productivity
We have adopted Kaizen, “Change for Good” in our center
We have Kaizen meeting once in 3 months along with our quality meetings. The staff were
encouraged to submit basic idea cards which are discussed, opinions from all staff members
is sought and the best possible ideas are implemented. This not only results in improving
quality, reduction in wastages, it also helps in improving patient and employee satisfaction.
A Board is put where all the ideas generated, and stage of its implementation are displayed.
The implementation is tracked so that it is completed within defined time. All implemented
ideas are displayed on “Kaizen Wall of Fame”